How to choose the right method for testing medical devices for blockage
There are many important applications for blockage testing in the disposable medical device manufacturing industry. These include catheters, tubing sets, valves, needles, restrictors/regulators, microfluidic chips, respiratory components, suction therapy devices, and more.
The main methods used for medical blockage testing are as follows:
The main methods used for medical blockage testing are as follows:
- Backpressure occlusion blockage testing
- Minimum pressure decay blockage testing
- Mass flow blockage testing
- Controlled flow backpressure occlusion blockage testing
Backpressure Occlusion Blockage Testing
This test type utilizes a constant user-regulated air pressure delivered by the test instrument to the part under test. The test is simple and has only one operating step where at the end of a test timer, the backpressure is recorded and must remain below a high backpressure limit (as defined by the user) to pass. Unblocked parts typically have much lower backpressures versus parts that are blocked.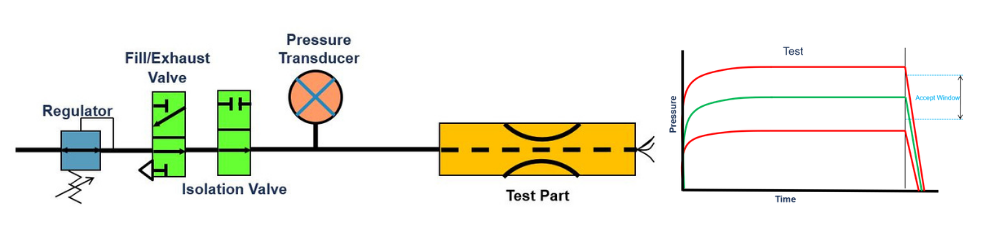
Advantages
- Ideal for parts where the smallest unblocked restriction in the air pathway is >3.0 mm diameter (larger openings).
- Simplicity in setup. Only one active step and easy-to-interpret backpressure results.
- Test is included on most CTS Sentinel instruments as standard. No added annual calibration cost.
- Test is also available with CTS Sentinel Differential Pressure Decay instrumentation, which allows for testing for small leak rates with greater repeatability as well as those same small leak rates on larger internal-volume parts.
Disadvantages
- Often poor to non-existent separation on parts where the smallest unblocked restriction is <3.0 mm diameter. Backpressures measured are relatively high on both blocked and unblocked parts in this range, so it can be difficult to get sufficiently definitive test results.
- Added complexity and steps to ensure the air pressure regulator has not been intentionally or unintentionally misadjusted by the user, allowing potentially blocked parts to pass.
- Test is not designed to detect partial blockages or grade the degree of blockage (ie. detecting different component diameters). Operates as an attribute-only test, identifying whether the part is completely/near-completely blocked versus unblocked.
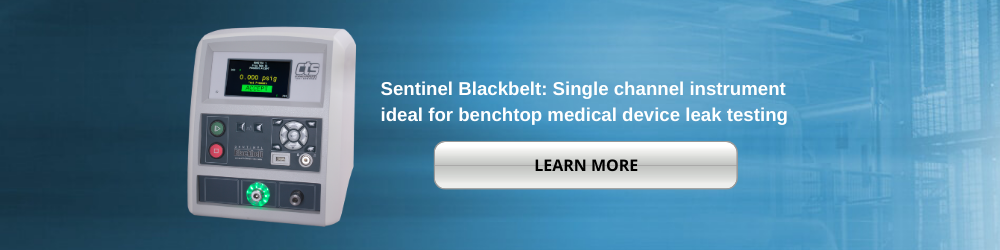
Minimum Pressure Decay Blockage Testing
This test type is somewhat similar to the Backpressure Occlusion test above, however the key difference is that after the user-regulated air pressure is delivered to the part under test, the instrument’s internal valves close, isolating the part from the pressure supply. Almost immediately, the instrument begins recording the loss of pressure through the part to atmosphere. The final decay over the user-defined test time is recorded and must fall below a user-defined decay limit to pass. Unblocked parts typically drop pressure rapidly versus parts that are blocked.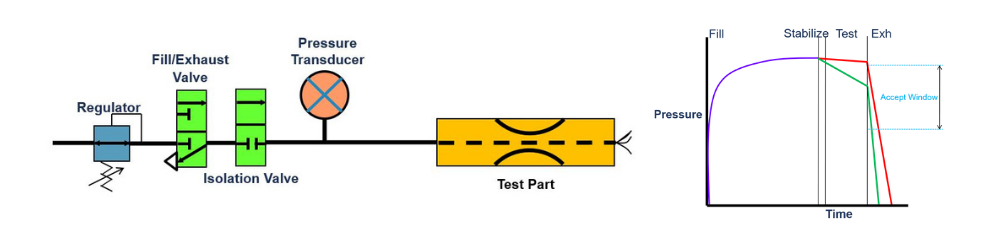
Advantages
- Ideal for parts where the smallest unblocked restriction in the air pathway is <3.0 mm diameter (smaller openings). Generally excellent for separation of blocked versus unblocked parts.
- An initial pressure window can be set during the Fill step to ensure the instruments pressure regulator was set properly.
- Test is included on all CTS Sentinel instruments as standard. No added annual calibration cost.
Disadvantages
- Can be difficult to deliver/maintain consistent pressures during Fill step (affecting test repeatability) on parts where the smallest unblocked restriction is >3.0 mm diameter. Part is so open to atmosphere that often very little pressure can be held on the part long enough to be repeatably measured. Also, can be difficult to ensure that the part was properly mated to the instrument before starting the test.
- Test is not designed to detect partial blockages or grade the degree of blockage (ie. detecting different component diameters). Operates as an attribute-only test, identifying whether the part is completely/near-completely blocked versus unblocked.
- This test is not intended for use with Differential Pressure Decay instrumentation due to the typically extreme pressure losses on most unblocked parts (exceeds differential pressure transducer range).
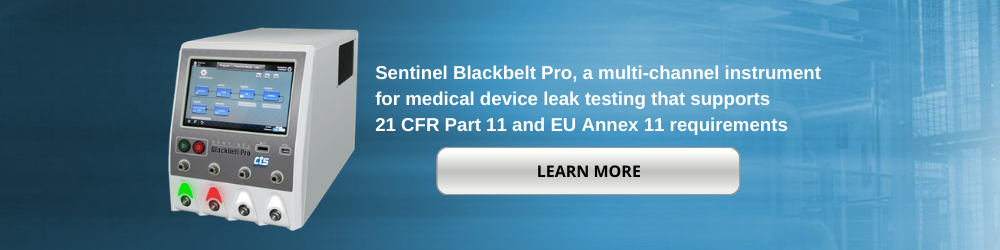
Mass Flow Blockage Testing
This test type utilizes a constant air supply during test similar to the Backpressure Occlusion test above, however instead of using only the pressure transducer, a mass flow transducer is incorporated into the circuit to make the final measurement. At the end of a user-defined test time, the actual flow value in sccm (standard cubic centimeters/minute) or slm (standard liters/minute) is recorded and must remain within minimum and maximum user-defined flow limits to pass. Parts with flow measurements outside the defined window may either have some degree of unintended blockage or instead involve assembly with incorrect components that have a larger or smaller pathway through the device to atmosphere.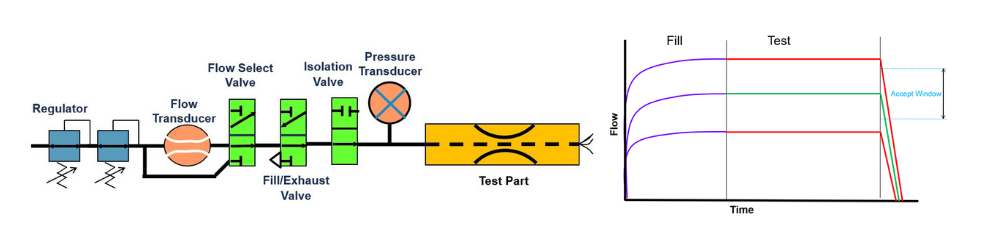
Advantages
- Ideal for detection of partial blockages and/or grading the degree of blockage of parts under test.
- This is the most sensitive blockage test using air available today.
- An initial pressure window can be set during the Fill step to ensure the instruments pressure regulator was set properly.
Disadvantages
- Added capital investment as this test requires added hardware (flow transducer and added regulators) and as a result, this test method is not available on all CTS Sentinel models.
- Added annual calibration cost due to the requirement to calibrate both the pressure and flow transducers.
- The flow transducer range must be sized properly for testing all part models/sizes that are required. If there are extremes in the restriction path design between different parts that must be tested (example: 0.25 mm smallest vs. 10.0 mm largest), this may require multiple instruments and/or test channels with each instrument/channel incorporating unique flow transducers ranged to measure at those varied flow values.
Controlled-Flow Backpressure Occlusion Blockage Testing
This test type is essentially the opposite of the Mass Flow test above in that the flow through the part is fixed (versus fixing pressure as found in the mass flow method) and the variable backpressure is measured (versus flow as found in the mass flow method) at the conclusion of the test and compared to user-defined minimum and maximum pressure limits. The constant flow is generated by a custom Flow Controller device added to the instrument which is designed to constantly measure and correct the actual flow through the circuit throughout the testing process. In almost all cases, this test is utilized in the inspection of disposable respiratory devices where the test specifications require measurement of residual backpressure with a fixed flow applied.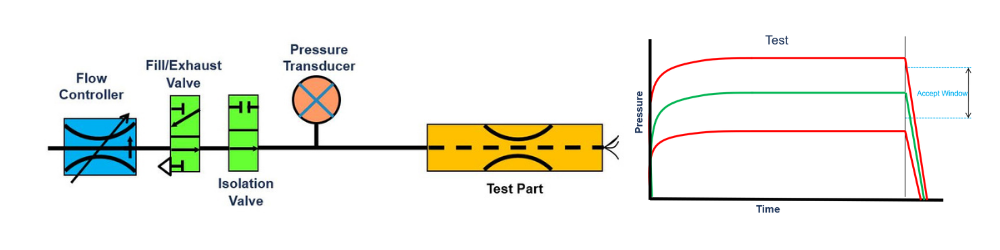
Advantages
- Capable to detect partial blockages and/or grading the degree of blockage of parts under test.
- Ideal when user-specifications require measurement of backpressure under a fixed-flow condition.
Disadvantages
- Added capital investment as this test requires added hardware (flow controller) and as a result, this test method is not available on all CTS Sentinel models.
- Added annual calibration cost due to the requirement to calibrate both the pressure transducer and flow controller to maintain optimal functioning.
- Added complexity and steps to ensure the flow controller is actually outputting the target flow value requested (ensuring no hardware issues/problems).
- The flow controller range must be sized properly for testing all part models/sizes that are required. If there are extremes in the mandated fixed-flow values of different parts that must be tested (example: 20 sccm minimum vs. 20 slm maximum) this may require multiple instruments and/or test channels with each incorporating unique flow controllers ranged to generate those varied flow values.