Cincinnati Test Systems (CTS) is an industry leader in the design and manufacture of functional leak test systems. Our test stations provide highly accurate test results, semi-automatic operation, and fully automated testing. They can also be customized to meet your application requirements, as demonstrated here. [caption id="attachment_177" align="aligncenter" width="491"]
This dual-station functional leak test system is designed to sequentially perform leak and performance testing on three models of turbocharger assemblies[/caption]
These modular roll-up test carts, are used for system changeover between three different turbocharger assembly models. Each model setup features a leak test tool cart and a performance test tool cart. The system is specially designed for quick and easy changeover without the use of tools. This functional leak test system requires only minimal operator interaction. The operator loads a part on the fixture plate, makes any necessary part connections, scans a bar code to validate correct part setup, and then initiates the automated test cycle. Testing begins and is performed from start to finish without operator intervention. Leak testing at Station 1 includes static testing of the turbocharger assembly’s compressor, turbine, and bearing housings. Performance testing at Station 2 includes high speed dynamic testing for speed, acoustic, vibration, compressor, VTG, WG, and NVH, as well as oil temperature, flow, and pressure monitoring, followed by end-of-test oil purge. Test cycle time is approximately 60 seconds.
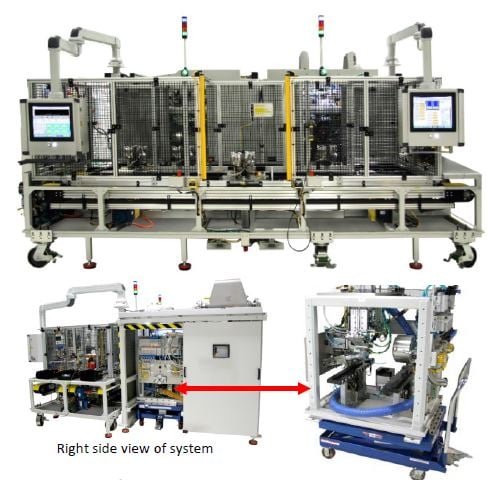
Turbocharger Assembly Cold Function Test Systems with Modular Tooling Changeover
This dual-station functional leak test system is designed to sequentially perform leak and performance testing on three models of turbocharger assemblies. Test parts are tested sequentially in two stations, one for leak testing (Station 1) and one for performance testing (Station 2). An automated fixture delivery system moves fixtured turbochargers from the part load station to the test stations and back to the load station for unloading after testing. The system can operate with a queue of four part fixture plates, which allows staging for continuous production. Preconfigured part fixture plates provide automated connections for automatic test cycles and fast changeover. Should a part fail the leak test, the system automatically bypasses the performance test station to deliver the rejected part to the load/unload station, reducing cycle times and maximizing throughput.
The Leak Test Systems Experts
CTS has been developing high performance, highly specialized function leak test systems for decades. We have the experience and expertise to develop a customized solution for your unique application. Request a quote on one of our functional leak test solutions, or contact CTS for more information.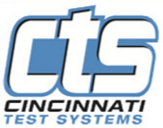