Battery Enclosure and Coolant System Sequential Leak Testing
Battery enclosures with cooling circuits require independent testing conducted to verify that cooling passageways do not leak fluid into the enclosure chamber. Utilization of sequential testing is simple when utilizing the Sentinel I28 leak test instrument. See the case study below for an example of an application.
Case Study: Battery Enclosure Cavity and Cooling Circuit Leak Test
A supplier of two different battery enclosures designs needed to conduct a leak test for the enclosure cavity and a cooling circuit in the enclosure at a different pressure. Cincinnati Test Systems supplied a turnkey test system with tooling designed to seal and leak test the two different die cast battery enclosure designs. One part had a larger footprint than the other part, beyond that they were leak tested with similar reject criteria.
The battery enclosure consists of a main battery enclosure cavity and coolant passageways. The coolant passageways were combined into one test and the cavity needed tested independently at a different pressure from the combined coolant passageways. CTS utilized the Sentinel I28 pressure decay instrument with two pressure sources, high flow valves for filling and exhausting large cavities quickly, and sequential testing that allows conducting two independent leak tests while supplying test data for each test stored and reported for the same part design.
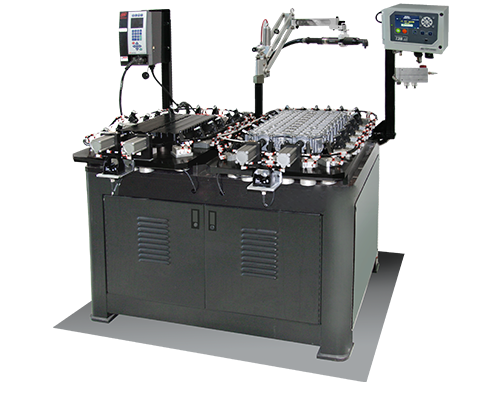
The test system tooling provided two independent fixtures, each built onto a main tooling plate. Each test fixture included filler blocks to load the battery enclosure over (filler blocks remove test volume allowing quicker test cycle time). A seal gasket followed the entire periphery of the enclosure edge designed similarly to the mating surface of a battery cover. Clamping force is supplied by clamps positioned to contact the enclosure at each of the fastener locations with enough force to seal and hold the enclosure in a fixed location throughout the leak test cycle without movement. Inlet and outlet coolant ports were sealed by pneumatically actuated cylinders with flat face and bullet nose molded seals.
CTS integrated the Sentinel I28 into this test system and utilized the instrument I/O controls to actuate the pneumatic sealing functions of the system without the need for PLC integration. Upon test completion the instrument includes green accept lamps and red reject lamps with an operator display identifying the final test measurement for operator notification of the test sequence and completion of the test.
Need your die cast parts tested?
Contact CTS if you have similar requirements for conducting testing on die cast parts. Our team will work with you on the final requirements of your production testing needs to quote, design, and build an economically efficient test system for your application.