Dunk and Bubble Leak Testing Systems
Dunk and bubble leak testing is a method of testing a part vessel or cavity for leaks by submerging it in a water tank. The part is filled with gas—typically compressed air—and leaks are identified by an operator monitoring whether a stream of air bubbles escapes from the part. The size and of the bubbles and rate at which they can both signify the size of the leak.
How a Dunk Tank Bubble Leak Test Works
Pressure decay dunk tests test the tightness of sealed parts for compliance with specifications and to ensure product quality. Seal integrity is especially important for parts containing gases, fluids, and flammable or corrosive substances. Having a tight seal is also important for parts that could be damaged by the penetration of soapy water, fluids, or contaminants.
Dunk tests are often used to help identify leakage issues prior to final assembly. They are best for smaller components because of the tank size and to make it easier to monitor leaks. Because of the fluids involved, dunk tests should not be used for components that are sensitive to moisture.
Extreme care must be taken when dunking the part into the tank to prevent air bubbles from being pulled down, creating the illusion of a leak. It is also important to maintain proper air and water temperatures during the test to allow for proper pressure stabilization and ensure accurate test results.
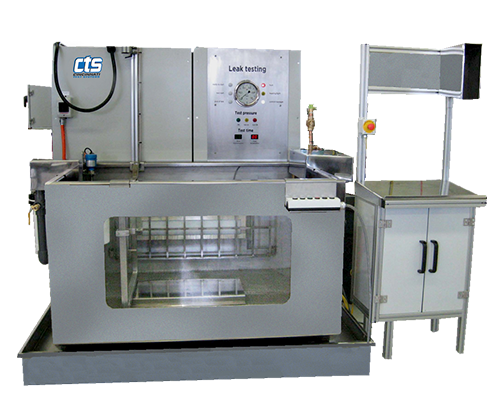
Advantages and Disadvantages of Bubble Leak Testing
Dunk testing is the simplest method of leak testing but it comes with its own pros and cons.
Advantages
- Simple and effective testing method to certain leak rates
- Reports pressure or flow loss
- Determines leak rate based on pressure
- Automated gross leak testing can be managed with instrumentation
Disadvantages
- Difficult to scale for production
- Operator-dependent, which can affect results
- Exact metrics not available, making it difficult to optimize testing
- Large footprint compared to other leak test solutions
- Wet, potentially destructive, test method
Convert Dunk Testing from Bubbles to Measurable Leak Testing
In this popular blog post, we talk about leak rates and provide an overview of how dunk tank testing pressurized or sealed parts works.
Components of a Dunk and Bubble Test System
A dunk and bubble test system performs a gross pressure decay leak test on the interior of the vessel and uses pre-pressure measurement and pressure measurement of time to identify a gross leak. The dunk test system can include:
- Manual and automatic operation
- Fixturing to secure the part for part handling (loading and unloading large parts)
- Sealing the part for test pressures
- Plumbing
- Regulation of compressed air
- Booster air systems to achieve test pressure
Dunk testing requires a protective enclosure for the operator, as some parts are tested under extremely high-pressure.
In some applications, the dunk leak test system will provide seal components to cover and seal large ports in the part, holding the test pressure without leaking. This type of system is custom designed to part design and used for: testing fitting, valves, weldments, fuel tanks, powertrain components, faucets, water heaters, gas cylinders, boilers and more.
Leak Rates for Dunk Tested Parts
The simplicity of the dunk tank is counting the bubbles. However, this also indicates the test sensitivity that can be expected. For example: if you have two bubbles per minute that equals a leak (flow) rate of .03 cc per minute. If you have 10 bubbles in a minute, that’s a flow rate of 0.14 cc per minute. Thirty bubbles per minute is in the 0.5 cc range. Once we are at a flow rate of 1 cc per minute, that’s 70-75 bubbles per minute. With a rate this high, it’s difficult to achieve repeatability with dunk testing for most applications.
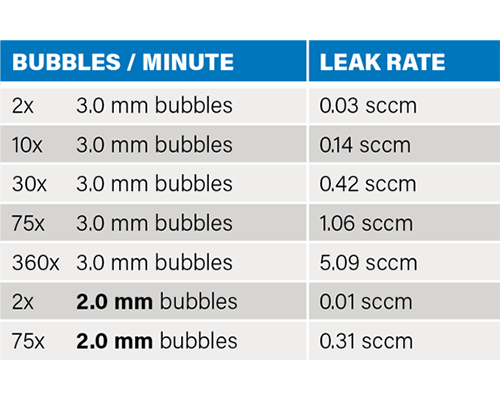
Contact CTS for Dunk Leak Testing Systems
For your next project let Cincinnati Test Systems will custom design a turnkey function test system for your parts. Contact us to discuss options for our customized dunk test systems and other leak testing solutions.