Differential Pressure Decay Leak Detection with Leak Standard Calibration
A differential pressure decay with leak standard leak test uses high precision dP pressure decay technology to test for a leak by measuring a differential pressure between a reference volume and the test piece calibrated to a standard volumetric flow. This test uses a differential pressure transducer to measure pressure loss correlated to a flow rate in scc/m.
Differential Pressure Decay Leak Standard Calibration Cycle
To prepare for calibration, the instrument must be set up for the correct test pressure and a repeatable leak testing sequence that includes fill, stabilize, isolation, test, exhaust and relax timers. This process is conducted manually by verifying filling the part to stable pressure, identifying the time for becoming stable, setting the isolation timer to 50% and achieving a 2:1 difference between known leaking parts and a non-leaking part.
Once complete, the operator will utilize a master part placed into the test fixture and press the instrument auto-calibrate button:
- A non-leaking master part is tested to establish the “zero leak” setpoint (master part loss)
- The master part is tested with the leak standard included in the test circuit to determine the maximum acceptable leak rate (master plus leak loss)
Using these setpoints, the leak test system establishes the “target flow window” for differential pressure decay leak detection.
Test Cycle
The test cycle fills a test part and a reference volume to a specified test pressure, the air source is cut off by the fill valve, test pressure stabilizes, and a reference air isolation valve is closed as the exhaust valve is open, isolating pressure on both sides of the differential pressure transducer. The transducer measures the pressure on both sides of the transducer throughout the test period. At the conclusion of the test, the instrument calculates the volumetric flow rate in scc/m based on the pressure loss measurement and test time . If the flow rate is within the “high and low limits window, the part passes the leak test. If outside the target limits, the part fails the leak test and is rejected. See diagram.
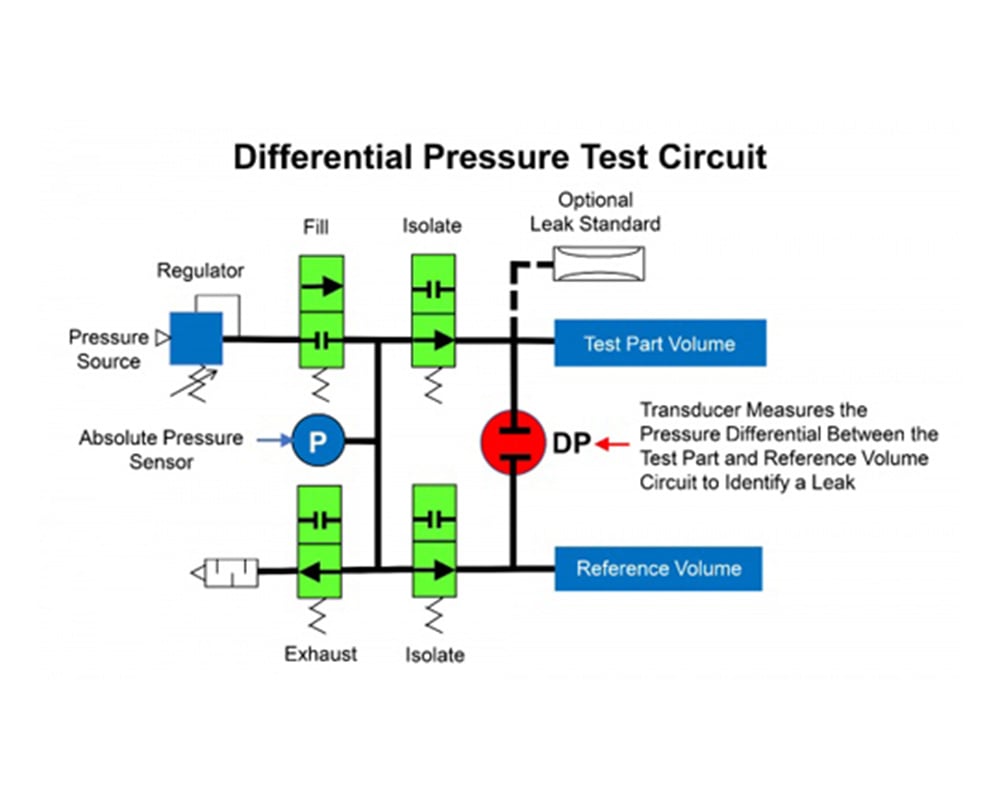
Tips to Setup and Validate a Reliable Calibration
There are important factors to be considered to conduct and validate a reliable calibration:
- It is important to utilize a known non-leaking production part as a master part
- The leak standard should be certified and within its dated certification window
- The relax timer should be long enough for the master part to exhaust fully and achieve ambient temperature status
- Check the final performance factor “PF” instrument feedback to verify the calibration cycle is acceptable
- Utilize master “good” and master “reject” parts with leak standards below and above the reject limits to validate a calibration process
Have questions about these factors?
Reliable and Accurate Differential Pressure Decay Leak Testing
Cincinnati Test Systems provides high precision differential pressure decay leak test systems: Sentinel MH, LPC 528, Sentinel C28, Blackbelt, Blackbelt Pro, and Sentinel I28. We are happy to help you determine which instrument best meets your differential pressure decay leak testing needs.